Case Study: Grinding Circuit Re-Lines
Overview
We have been providing complete bolting solutions for over 30 years to the Mining, Refining, Hydrocarbon, Power Generation, Marine, Motor Vehicle, Construction and Fairground Industries.
The foundation of our knowledge base has been built by measuring the actual bolt tension achieved by any tightening method. This has given rise to a knowledge base that has driven the solutions that we now provide, the two key factors are: Ultrasonic Bolt Tension Measurement & Joint Analysis Management
Discussion
The process of re-torquing after a re-line is very common. It has been a necessity to reduce the number of failures however it doesn’t need to be that way.
In order to find the solution we first had to fully understand all the contributing factors.
Top 3 Root Causes of Failures
1. Pre-load too low
The interfaces between the bolt, liner & shell are rarely smooth or machined, consequently the friction is greater than standard calculations consider, consequently the standard formula often results in low average bolt tension.
2. Inconsistent service processes
Consistency is a bigger factor than most realize. The relationship between torque tightening and bolt tension in good conditions is generally regarded as +/- 25%. Add rough surfaces, interaction and short clamp length to diameter ratios and this becomes significantly higher. Our experience is that the variation becomes more like +25% - 100%; it is rare when we measure all bolts that we don't find at least one that is completely loose.
3. Relaxation too high
We have found that the relaxation on liners is particularly high. The mating surfaces between the lifters, liners and liner bolts have many high spots being rough cast and forged. Added to this the tapered engagement at the inner end of the bolt multiplies any relaxation. Any small embedment of high spots will be multiplied by the slope angle. By way of an example if 0.1mm embedment occurs on a 1:4 taper that will result in 0.4mm in lost elongation. That is a likely scenario when both sides of the slope are considered.
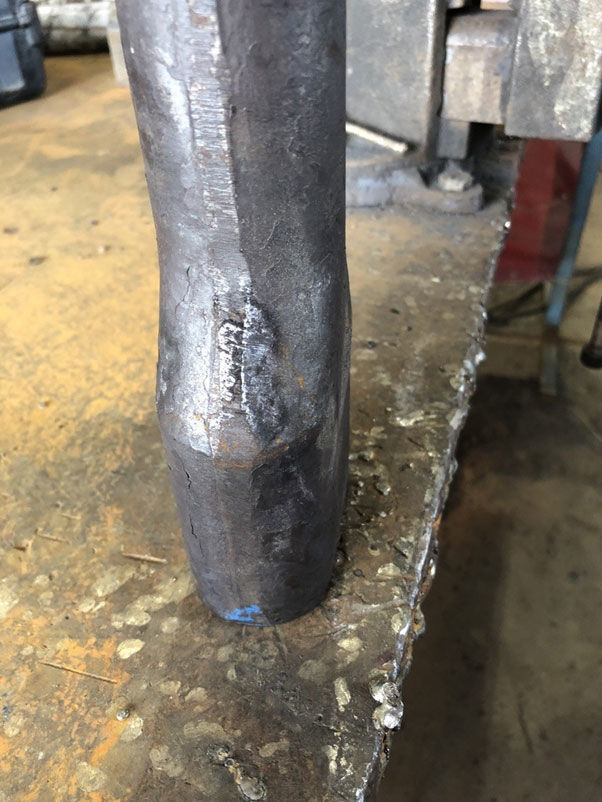
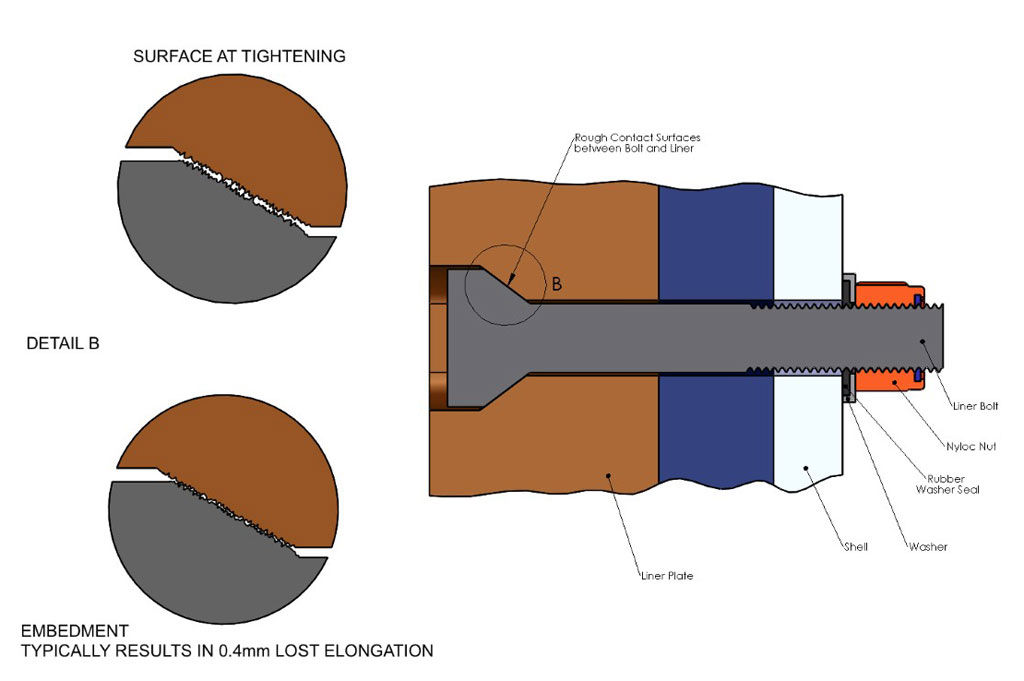
Liner bolts fail (break or loosen off) for several reasons but our extensive experience demonstrates that these can be eliminated if the pre-load is correct. Fatigue failure is the most common mode; this is almost invariably due to pre-load that is too low. The reasons for this can in turn be divided into 3 groups, inadequate original tension, inconsistent tension and high relaxation.
To eliminate this we measure and adjust every bolt to precisely the required bolt pre-load. Many companies fear that this will slow down the process but because our people do this constantly they are very quick and we reduce the time taken.