Time is money in any industry.
When your machinery fails to undergo periodic tests and checks, unexpected downtimes are inevitable.
Such is the case with liner bolts that have accumulated a number of failures in the past.
The question is, how does it happen, why does it occur, and what can be done to prevent it from causing problems in the future?
Boltstress Ultrasonics got to the bottom of this situation and conducted a thorough ultrasonic bolting measurement and analysis of the Mills in question. This task led to numerous revelations, which is presented in this post.
Design Calculations:
In this particular task, the G5 Bolt Tension Monitor by Boltstress Ultrasonics was utilised by the specialist bolting engineer to determine the cause of failure.
Calculations of the component strengths determined that the target tension equated to the following:
Bolt = 30% yield strength
C-track = 75% yield strength
Observations
It was noted that various issues have occurred:
Washers
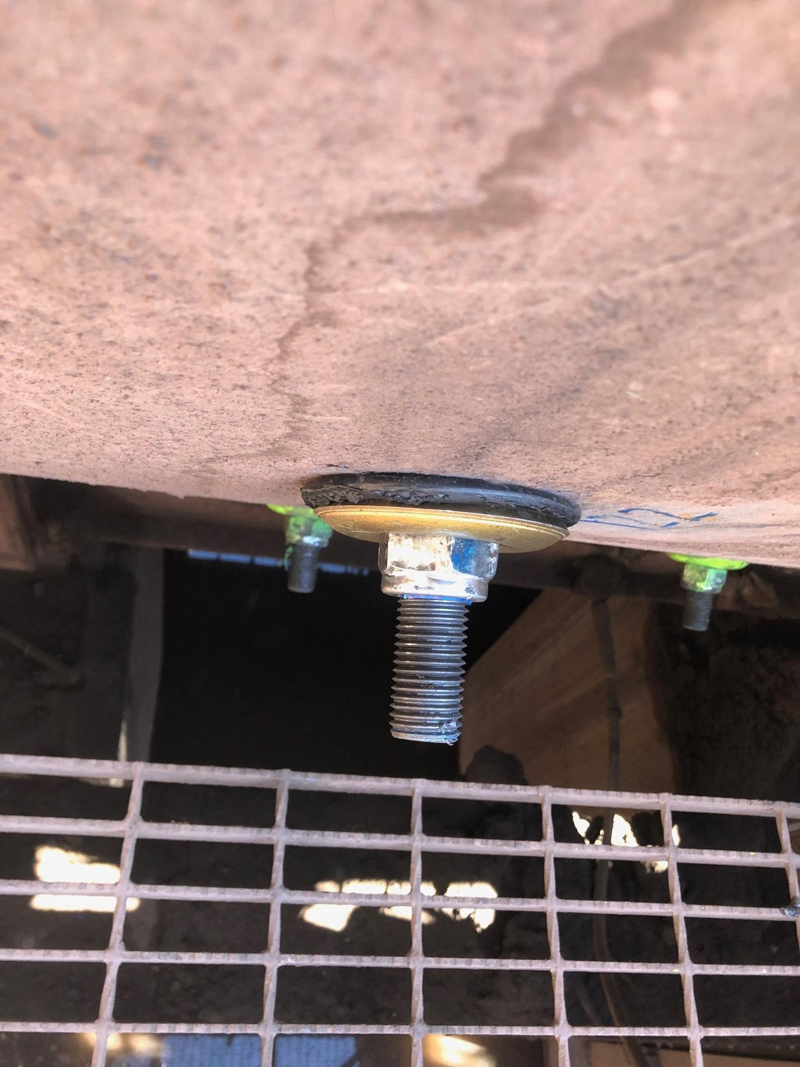
After inspecting and analysing the condition of the washers, about 30 percent of the cup washers significantly collapsed under tension.
Bolt Alignment
In a number of cases observed, the pressed or forged type washers did not sit flat onto the shell. Albeit only a single row, the machined type did not appear to possess a similar issue.
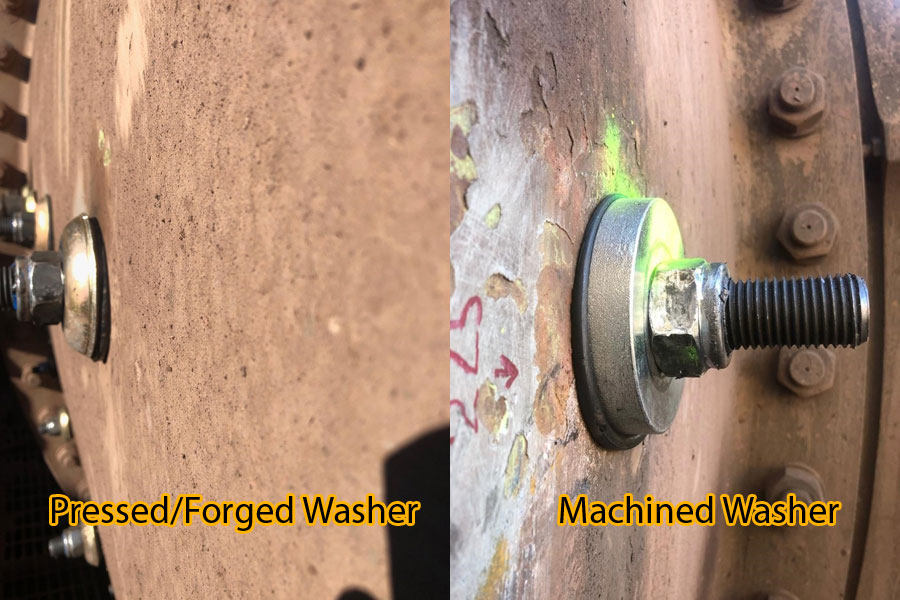
Torque Settings
A previous process had used Torque figures of 650, 700 & 750nm. Whilst we used the higher figure, this was only applied by utilising a hand wrench.
This brings into play the effects of static vs dynamic torque, consequently the applied torque required to reach our target tension was between 750nm & 1050nm. This is a normal variation (scatter) that we experience between applied torque and residual bolt tension.
Torque Sockets
Due to the high thread protrusion above the nut, reline crews carry out modifications to sockets by welding in spacers to compensate for this. These are rarely, if ever, proof tested to the required torque, consequently the failure rate is high. There was one such instance.
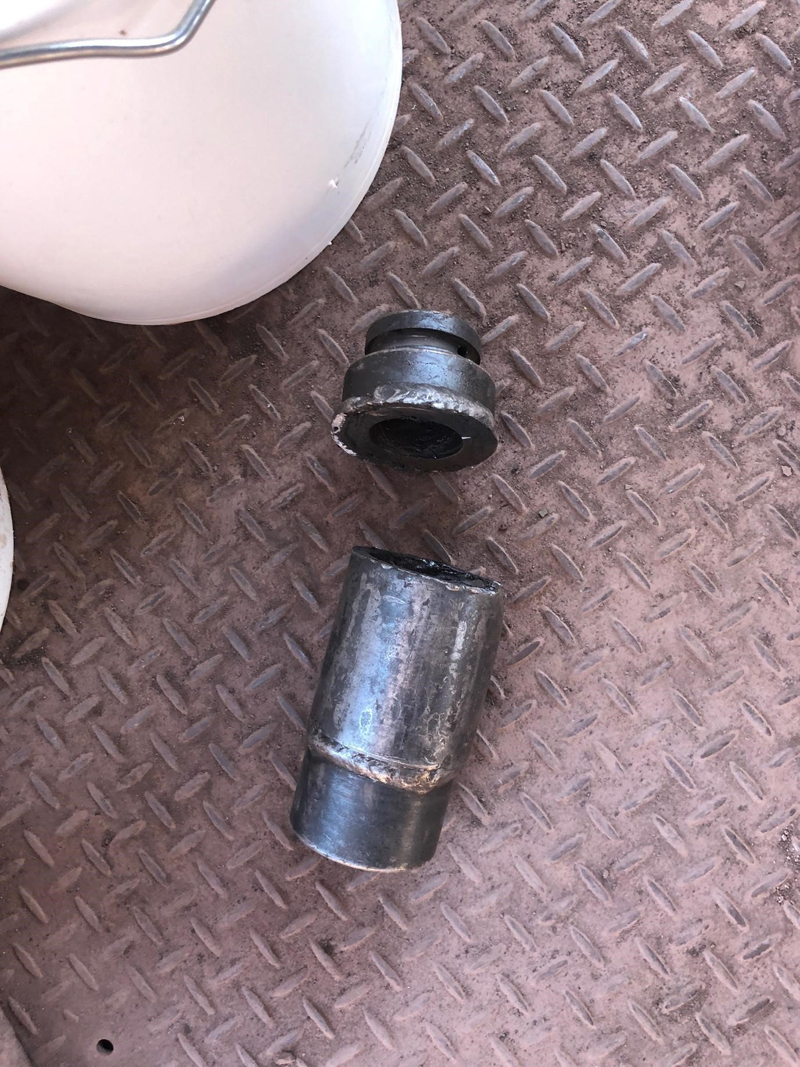
Post Ultrasonic Bolting Measurements and Analysis Recommendations
After a thorough analysis of the bolts and nuts, we have come to the following recommendations to prevent future and recurring failures:
-
Washers: The forged/pressed type Cup washers collapsed at relatively low tension. The trialled row of machined washers also began to deflect, probably beyond the elastic limit. Thickness, diameter and hardness increases are being considered.
-
Lifter Bar C Track: With these arrangements, it is normal that the interface between the T section of the bolt and the C-track are the factors that govern the allowable bolt tension. The Multotec bolts have a thicker T section than we have seen elsewhere, this gives a much higher overall strength of the bolt. A similar thickness of C-track would allow much higher bolt tension to be initially applied. This could lead to elimination of the need to re-torque 12-24 hours after startup.
-
Further testing should be carried out during the next re-line, with the intent of eliminating both the re-torque process and the bolt failures.
-
Torque Tube OEM manufactured sockets will eliminate the failures of the existing site welded types. We have passed the details of the OEM for these to the client for consideration.
Summary of Ultrasonic Bolting Measurements and Analysis
We have arrived at three significant findings after conducting ultrasonic bolting measurements and analysis. The accuracy of the torque to tension relationship for the current status is inadequate. The nuts & washers need to be improved. There is plenty of scope to eliminate the re-torque.